
MR. HYDRODIP SOUTH AFRICA
WE DO IT BEST
Take your old, used or even new parts and have them transformed into the customised option of your choice. All workmanship and quality guaranteed. We do refurb work and custom spray jobs as well. Old damaged dashboards? No problem, we will make them look as good as the day they were made.
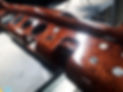
WHAT IS HYDRO DIPPING?
Hydro dipping is a water transfer of graphics onto almost any substrate from woods, steels, aluminum, plastics and even onto glass.
WHAT WE OFFER
The latest in water transfer printing/hydro graphic technology, that allows amazing patterns to be applied to almost any 3D surface. ALMOST ANY SUBSTRATES OR HARD SURFACE MATERIAL CAN BE COATED. Be it glass, wood, metal, fibre glass, and plastics.
​
All work includes a epoxy primer / 3 base coats / Hydro dip / clear coat which is UV and chip resistant. Custom spray jobs. Wood grains, skulls, cartoons, animal prints, carbon fibre and forged carbon. Heat resistant up to 200 degrees celsius.
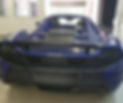

THE TECHNOLOGY
The substrate piece to be printed first goes through the entire painting process: surface preparation, priming, painting, and clear coating. After painting but before clear coating, the part is ready to be processed. A polyvinyl alcohol hydrographic film, which has been gravure-printed with the graphic image to be transferred, is carefully placed on the water’s surface in the dipping tank. The clear film is water-soluble, and dissolves after applying an activator solution.
Once dipping is begun, the surface tension of the water will allow the pattern to curve around any shape.[citation needed] Any remaining residue is then rinsed off thoroughly. The ink has already adhered and will not wash off. It is then allowed to dry.
The adhesion is a result of the chemical components of the activator softening the base coat layer and allowing the ink to form a bond with it. One of the most common causes of a failure to achieve adhesion between the two layers is a poorly applied activator. This can be either too much activator being applied or too little.
WHAT WE DO
THERE ARE 5 IMPORTANT PROCESSES

STEP 1
SURFACE CLEANING
We clean and degrease the part and make sure it is free of debris.

STEP 2
PRIMER
We prime the part you want us to dip, we us epoxy primer which is military specification.

STEP 3
BASE COAT
After the prime coat has dry complete we will start with the base coat. The base coat will be the primary colour of the part you would like to dip.

STEP 4
APPLICATION OF HYDRO PRINT
We gently place the film (pattern you selected) onto the water, then we spray a chemical called activator to dissolve the plastic of the film. After 10 seconds we start to submerge the part into the water, making sure every corner is covered.

STEP 5
CLEAR COATING
Lastly we spray on a clear coat, we can either make it a gloss clear coat or a matt clear coat. The choice is yours.